Setting New Industry Standards with the Best Cnc Turning Machine
In the rapidly evolving manufacturing landscape of 2025, the demand for precision and efficiency is driving the adoption of advanced technologies in machining. Among these innovations, the CNC turning machine stands out as a critical component in setting new industry standards. According to a recent report by MarketsandMarkets, the global CNC machine market is projected to reach $100 billion by 2025, with CNC turning machines playing a pivotal role in this growth due to their capability to produce complex geometries with unparalleled accuracy.
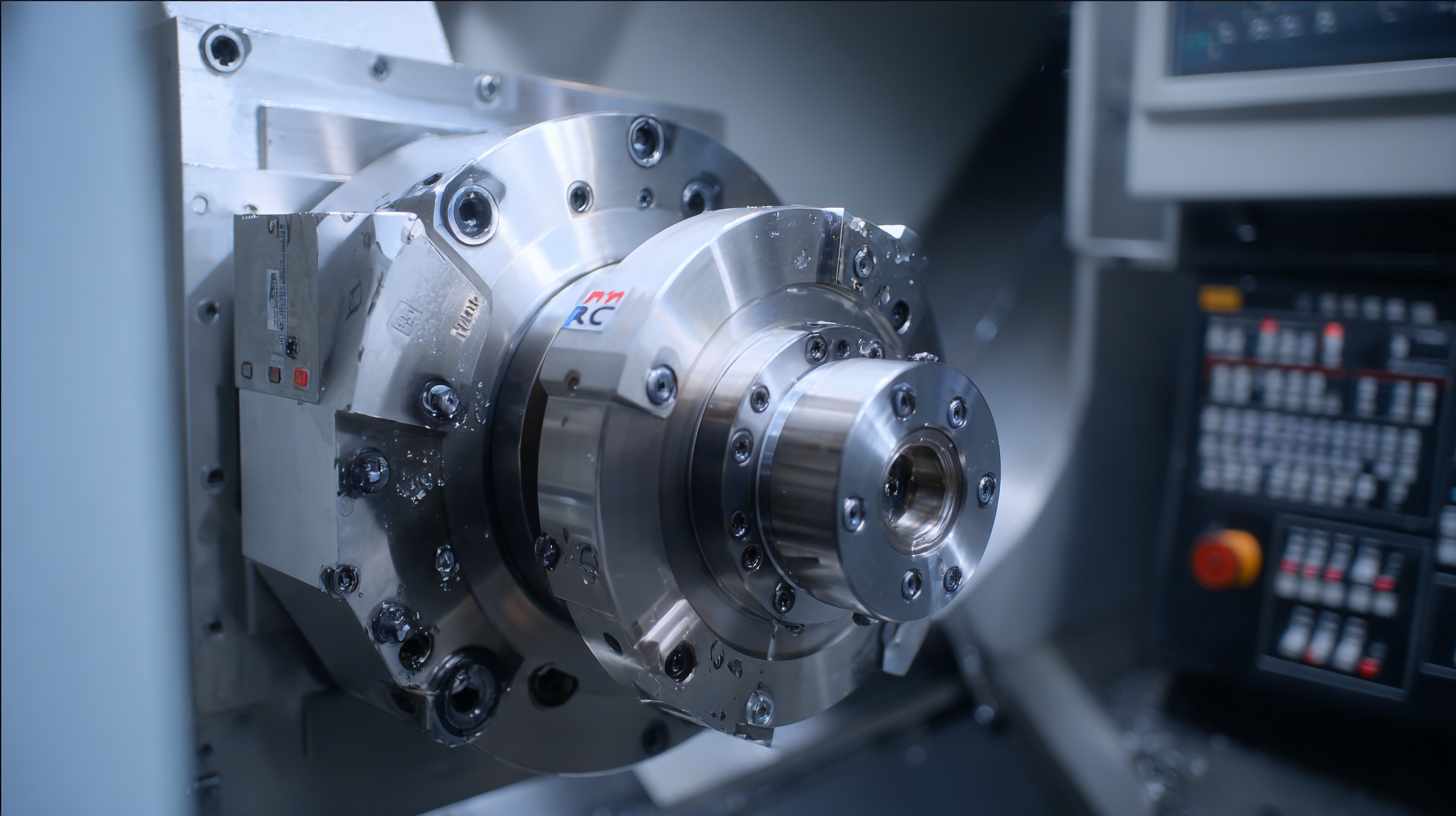
As industries increasingly prioritize automation and productivity, the advancement of CNC turning machines will not only enhance operational efficiency but also reshape manufacturing processes across various sectors, including aerospace, automotive, and healthcare. In this blog, we will explore how these state-of-the-art machines are leading the charge in redefining industry benchmarks and fueling innovation in manufacturing.
The Evolution of CNC Turning Technology: A 2025 Perspective
The evolution of CNC turning technology is poised to reshape industries by 2025, driven by advancements in automation and artificial intelligence. As manufacturing processes integrate more sophisticated CNC machines, the focus shifts toward enhancing precision and efficiency. Recent developments in the CNC machine market indicate a projected growth from over $101 billion in 2025 to nearly $196 billion by 2032, highlighting a robust compound annual growth rate. This surge can be attributed to the increasing demand for high-precision, multi-axis machining capabilities, which are essential for modern production environments.
Innovations such as twin-spindle CNC turning centers aim to redefine bar-fed machining applications, offering remarkable speed and accuracy. As companies leverage automation to streamline operations, the incorporation of AI technology is further catalyzing market transformation. Industry players are increasingly recognizing the potential of advanced CNC solutions to elevate productivity and meet the rising demands of precision engineering. With the market on the cusp of a technological renaissance, the next few years will bring unprecedented changes, setting new standards that will redefine manufacturing workflows.
Evolution of CNC Turning Technology: Market Share by Technology Type (2025)
Key Features to Look for in the Best CNC Turning Machines
When selecting the best CNC turning machine, several key features should be prioritized to ensure optimal performance and efficiency. One of the most critical aspects is the machine's precision. Look for models that offer high accuracy in their specifications, as this directly impacts the quality of the finished products. Advanced CNC turning machines often come with enhanced spindle designs and superior bearing systems, which contribute to improved stability and reduce the likelihood of errors during operation.
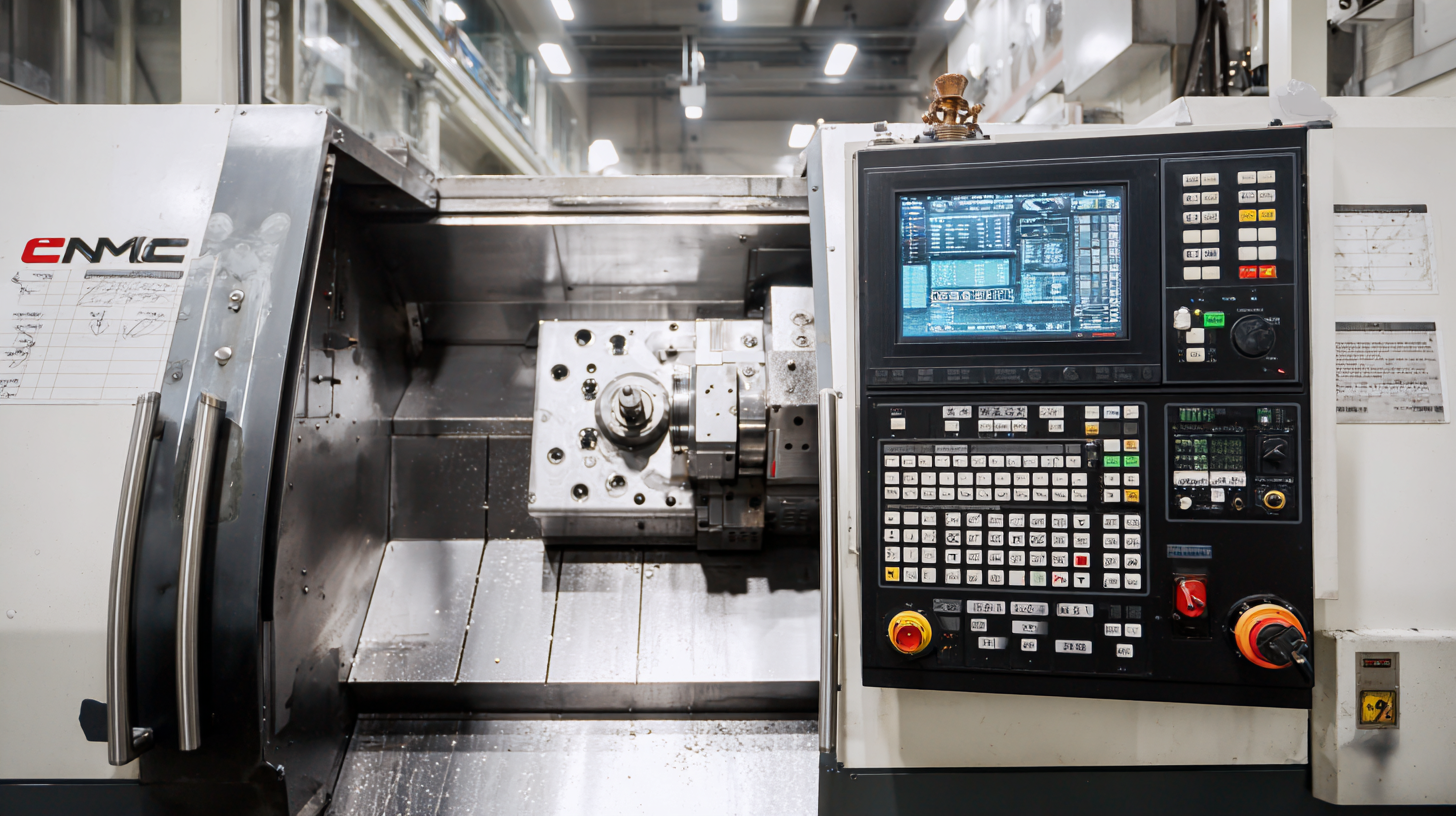
Another essential feature to consider is the machine's versatility. A top-tier CNC turning machine should be able to handle a variety of materials and complex geometries. This flexibility allows manufacturers to adapt to diverse production needs without investing in multiple machines. Additionally, features like live tooling and multi-axis capabilities enable operators to perform various operations in a single setup, further streamlining the production process. Investing in a CNC turning machine with these capabilities can significantly enhance operational efficiency and reduce lead times in manufacturing.
Innovative Materials and Techniques Transforming CNC Turning
The realm of CNC turning is experiencing transformative advancements through the adoption of innovative materials and techniques. Recent studies indicate that the global CNC machine market is projected to reach $100 billion by 2025, underscoring the increasing demand for precision machining. Modern CNC turning machines are now utilizing advanced materials like titanium alloys and composite materials, which not only improve strength-to-weight ratios but also enhance machining efficiency. This transition significantly reduces production costs while maintaining high-quality output, proving vital in industries ranging from aerospace to medical technology.
**Tip:** When selecting materials for CNC turning projects, consider factors such as thermal stability and wear resistance to optimize performance.
Additionally, the implementation of smart technologies—such as IoT sensors and AI-driven analytics—has revolutionized traditional CNC turning processes. These innovations allow for real-time monitoring and predictive maintenance, ultimately boosting productivity and minimizing downtime. According to a recent report, companies that adopt smart manufacturing processes can increase operational efficiency by up to 30%. As we continue to explore these cutting-edge techniques, it's clear that the future of CNC turning is not only about precision but also about smart, sustainable manufacturing practices.
**Tip:** Regularly update your CNC turning machine software to ensure compatibility with cutting-edge tools and techniques, maximizing your operation's innovation potential.
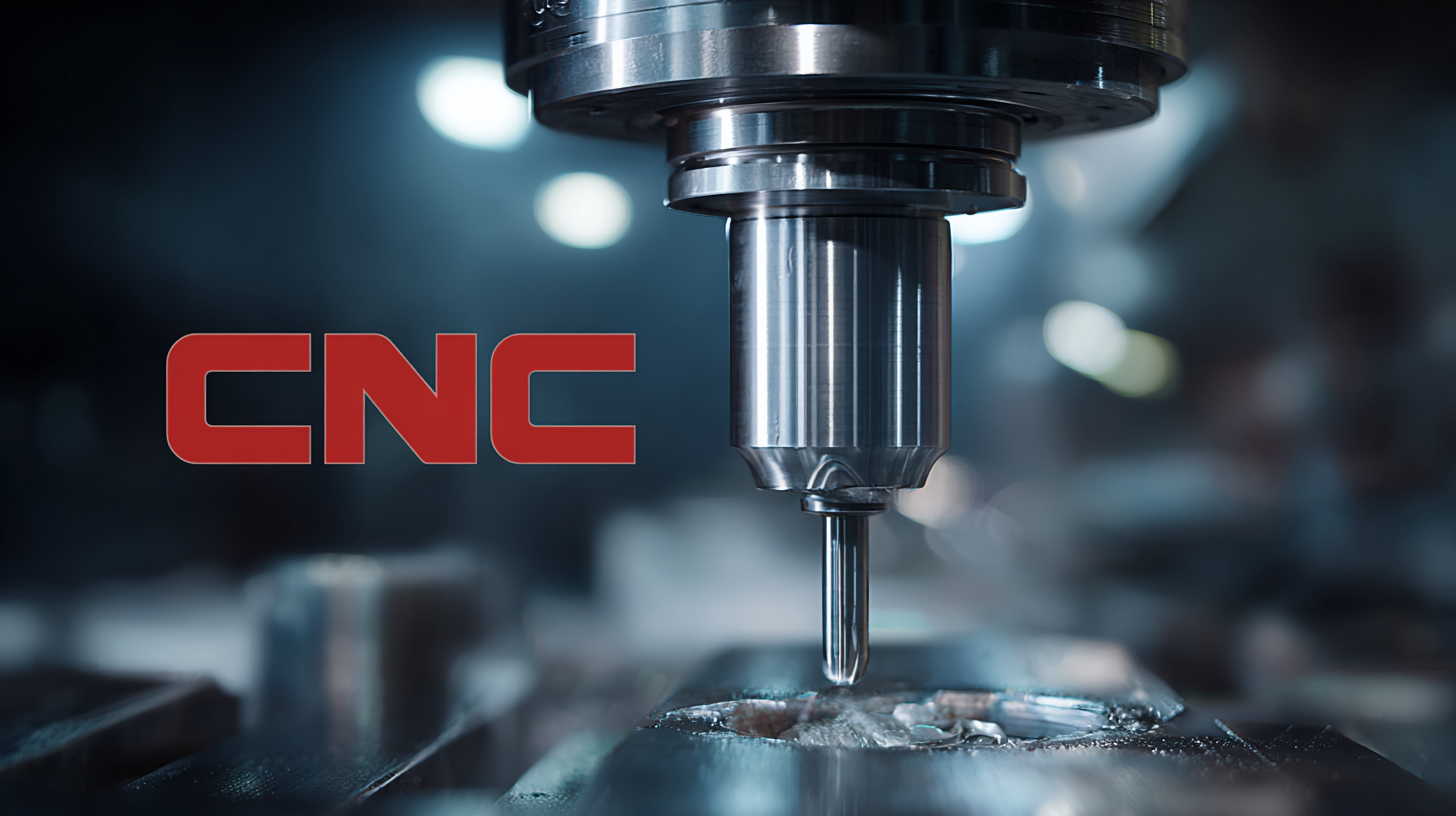
How to Optimize Your Operations with Advanced CNC Turning Solutions
In today’s competitive manufacturing landscape, optimizing operations with advanced CNC turning solutions is crucial for businesses aiming to set new industry standards. The global CNC machine market is projected to expand dramatically, increasing from $101.22 billion in 2025 to an astonishing $195.59 billion by 2032, reflecting a compound annual growth rate (CAGR) of 9.9%. This growth underscores the pressing need for manufacturers to invest in cutting-edge technology to enhance productivity and efficiency.
Implementing state-of-the-art CNC turning machines not only streamlines production processes but also significantly reduces operational costs. By leveraging these technologies, companies can achieve higher precision and faster turnaround times, meeting the evolving demands of the market. Additionally, the integration of automation and smart manufacturing practices facilitated by advanced CNC solutions helps businesses stay ahead of the competition, ensuring they can adapt to industry changes swiftly and effectively. As the market continues to grow, organizations that prioritize optimizing their operations will be well-positioned to lead the way in innovation and quality.
Future Trends: Integrating AI and Automation in CNC Turning Machines
The integration of AI and automation in CNC turning machines is revolutionizing the manufacturing industry, making it more efficient and capable of meeting rising production demands. According to a recent report from MarketsandMarkets, the global CNC machine market is projected to grow from $79.8 billion in 2021 to $113.3 billion by 2026, highlighting a compounded annual growth rate (CAGR) of 7.5%. This significant growth is largely driven by advancements in AI, which enhances the precision and adaptability of CNC turning processes, allowing for the production of intricate parts with minimal human intervention.
Furthermore, automation in CNC turning machines is enhancing operational efficiency and reducing lead times. A study by McKinsey & Company suggests that automating production processes can increase productivity by up to 20% within the first year of implementation. Incorporating AI algorithms in CNC turning not only optimizes tool paths but also predicts maintenance needs, significantly reducing downtime and operational costs. As manufacturers increasingly adopt these technologies, we can expect a shift towards smarter factories where integrated systems communicate seamlessly, resulting in unprecedented productivity and quality in manufacturing.
Setting New Industry Standards with the Best CNC Turning Machine - Future Trends: Integrating AI and Automation in CNC Turning Machines
Feature | Description | Benefits | Expected Adoption Rate (%) |
---|---|---|---|
AI-Powered Tool Path Optimization | Utilizes artificial intelligence to optimize cutting paths for efficiency. | Increased machining speed and reduced material waste. | 70% |
Real-Time Monitoring Systems | Sensors and software to monitor machine performance in real-time. | Enhanced troubleshooting and zero downtime. | 65% |
Automation Integration | Seamless integration with robotics for part handling and automation. | Improved operational efficiency and reduced labor costs. | 75% |
Predictive Maintenance Features | Analyzes data to predict machine failures before they occur. | Minimized machine downtime and extended equipment life. | 60% |
User-Friendly Interfaces | Intuitive control panels offering easy operation and setup. | Reduced training time and user errors. | 80% |
NORTH EASTON MACHINE • 218 Elm Street • North Easton, MA 02356 • 508-238-6219